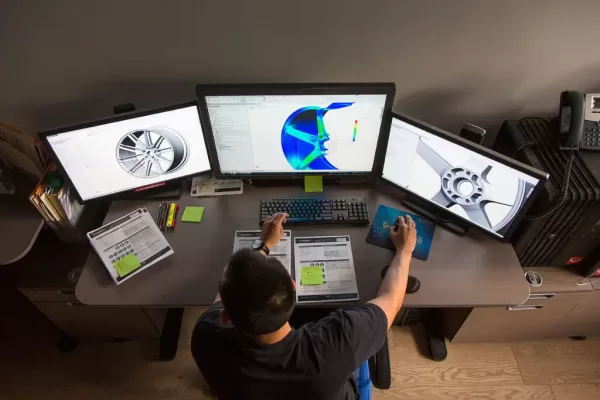
Design By Standards
We offer complete freedom of expression when choosing a design. You can choose forged wheels from the catalog or place an order for an individual design.
Every wheel goes through a rigorous design and development process, this ensures a precise end product that covers all the dynamic needs of our customers’ vehicles.
Every wheel goes through a rigorous design and development process, this ensures a precise end product that covers all the dynamic needs of our customers’ vehicles.
Every wheel design is physically tested in compliance with JWL, VIA and TUV standards. Using Finite Element Analysis (FEA) software each wheel undergoes simulated cornering, radial, and impact testing specific to the vehicle.
Forging The Blanks
The wheel blank is forged into the blank using a forging tool from the billet, which is made of 6061-T6 aluminum alloy. In each of the stages the blank is processed under 10,000 t pressure and heated between each step to retain the temperature necessary for forming. In stage 1 the billet is compressed into a disk. In stage 2 the disk is pressed in a special matrix to form a narrow wheel blank. Due to the extreme compression of the material, the blank possesses excellent mechanical properties and a very high-quality material microstructure.
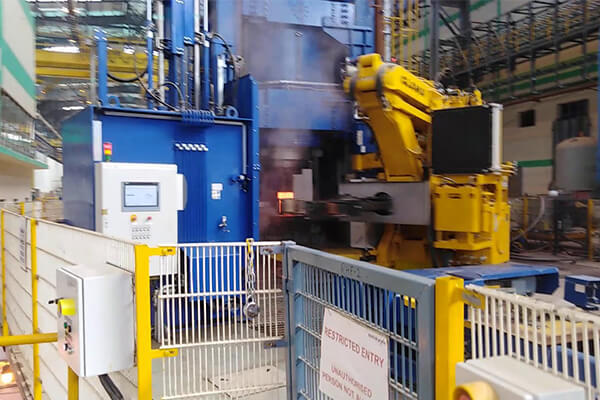
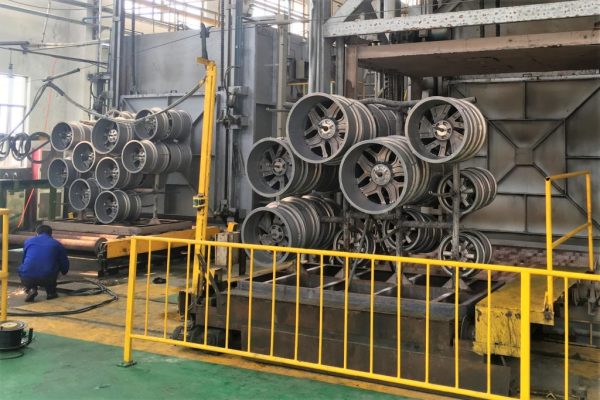
Heat Treatment
Solution annealing
Repeated strong heating, so-called solution annealing of the blanks, dissolves sufficient alloying elements in the molecular solid solution, allowing them to adopt a closer connection.
Quenching
Rapid quenching cools the blanks to 70°C and hardens the molecular structure. This reinforces the close bonds, but makes the wheel blank brittle at the same time.
CNC Machining
Highly-modern CNC machines finish the inside and outside of the wheel blank to the final dimensions. CNC machines remove as little as 0.01mm of material per pass to achieve the utmost precision.
Every wheel must go through the dynamic balance test. Only if the test is passed according to the extremely stringent tolerances is the wheel allowed to enter the rest of the manufacturing process.
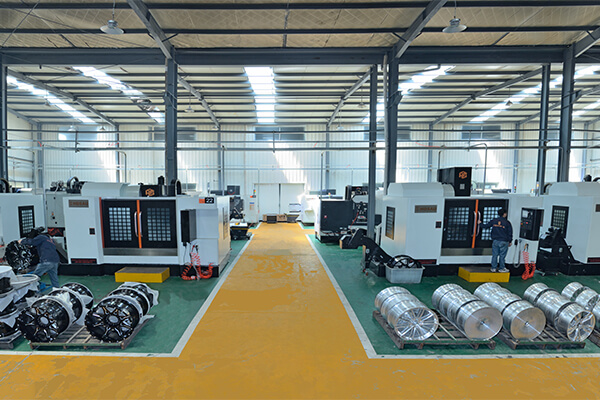
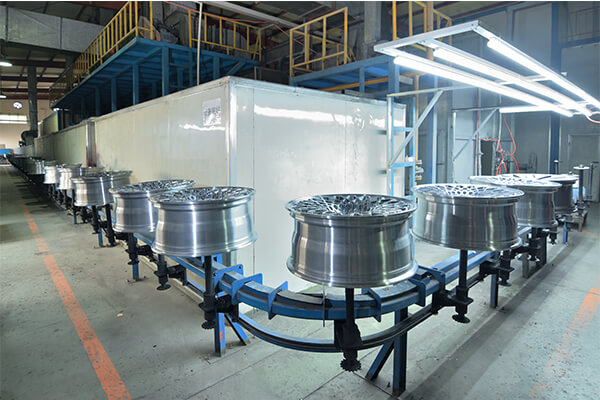
Finish
Comprehensive cleaning in the pre-treatment area removes all contamination on the wheel surface, which could potentially affect later lacquer application on the wheel.
Application of the colored paint onto the powder-coated wheel via electrostatic coating and compressed air spraying. This ensures even paint distribution even in difficult places, giving a perfect paint coating.
Final check of the surface quality by a staff member to ensure compliance with the high quality standards. The wheel then goes to be packed.